Helicopter landing in vessel decks is a critical operation due to multiple scenarios that can make the helicopter to be unstable during the landing.
This type of operations began to perform during the 40’s but, due to multiple accidents, in the 60’s it appeared the first standards to regulate these landings. As a result of the increment of the number of landings in offshore platforms (static as well as in movement), standards had to be updated continuously until nowadays, adding the most advance technologies to improve safety and to control helideck operations.
One of the taken actions to avoid landing accidents is that both, pilot and flight operator, must know several meteorological restrictions in which is not allowed to land, or where the landing must take lot of care. These operability limits are unique for each ship and each helicopter type, and they depend essentially on wind and temperature conditions.
Wind heading and intensity affect directly helicopter stability because strong gusts of winds produce so much turbulence in helidecks that it is impossible to operate.
Moreover, hot gases from ship exhaust funnels are also an important factor. If thermal rise between environmental temperature and gases temperature is high, the helicopter will experience lift changes that can cause high instabilities, putting the operation at risk.
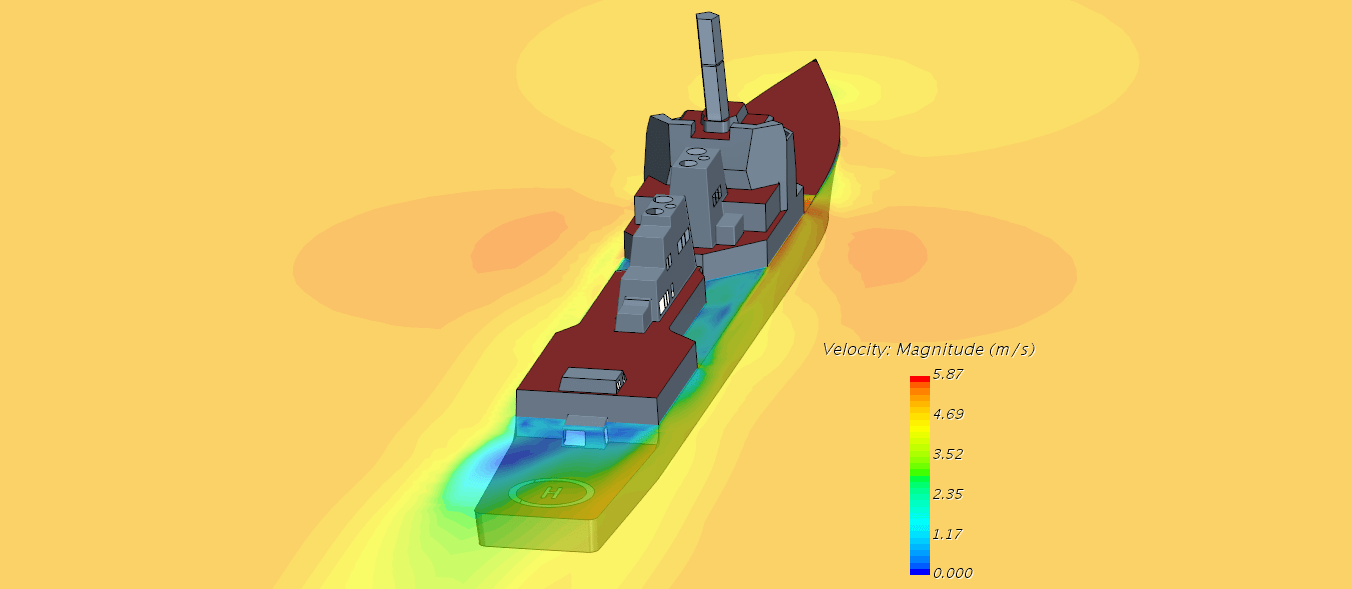
Because of this, helideck design must fulfil standards such as CAP437 or NORSOK C-004. These standards demand aerodynamic and thermal study in several scenarios to quantify turbulence and temperature values achieved near the helideck. Environmental conditions studied depend on multiple parameters such as ship operability, meteorological data and ship statics or movement.
Historically, this type of analysis used to be made with experimental test in wind tunnels. This method not only is more expensive and needs more time, but also it is limited in results and disturb the solutions due to the introduction of multiple sensors that modify air trajectory. Because of this, nowadays, thanks to computational capability advances, it is usual to develop computational numerical simulations to solve this type of problems.
CFD simulations are a very useful tool to develop these studies. They allow to reproduce the turbulence and temperature tendency that will experience the air close to the helideck. Air flow instabilities are produced by superstructure and thermal flow from exhaust funnels or by other thermal sources.
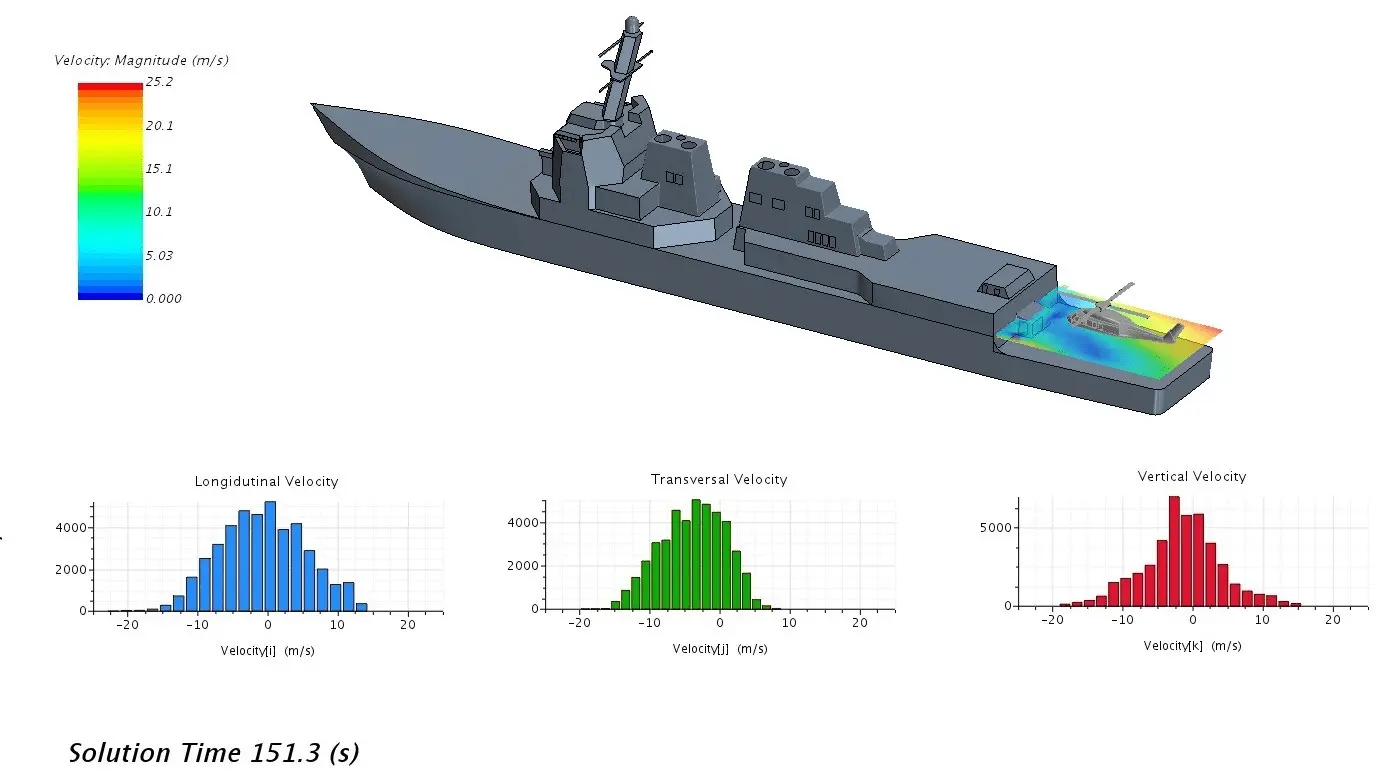
Dead work and superstructure geometry, exhaust gases conditions and sailing conditions during landing are needed to build the CFD model. Along with these data, it is created a numerical parallelepipedal domain of several ship lengths, where the ship is immersed. This geometrical domain has enough dimensions to analyze air flow effects in the helideck.
The most efficient helideck design strategy consists of doing CFD simulations in the earliest design stage. Thus, the helideck can be simulated in several positions with different configurations to quantify which one is less harmful and which one is available to operate more time in a year.
If the helideck position is already fixed, CFD simulations allow to study alternatives to mitigate both thermal and turbulence effect in landing zone. An example could be to set deflectors in the funnels outlet to guide hot gases to another direction or to modify, if possible, the location of superstructure objects that produce harmful vortices.
CFD tools properly applied by expert engineers allow to do a detail analysis of different aerodynamic problems that can be found in a ship and to evaluate efficient solutions in our virtual model to act quickly. This CFD tool applications belongs to the VICUSdt services portfolio in the tween model area.
More information:
Contact: info@vicusdt.com
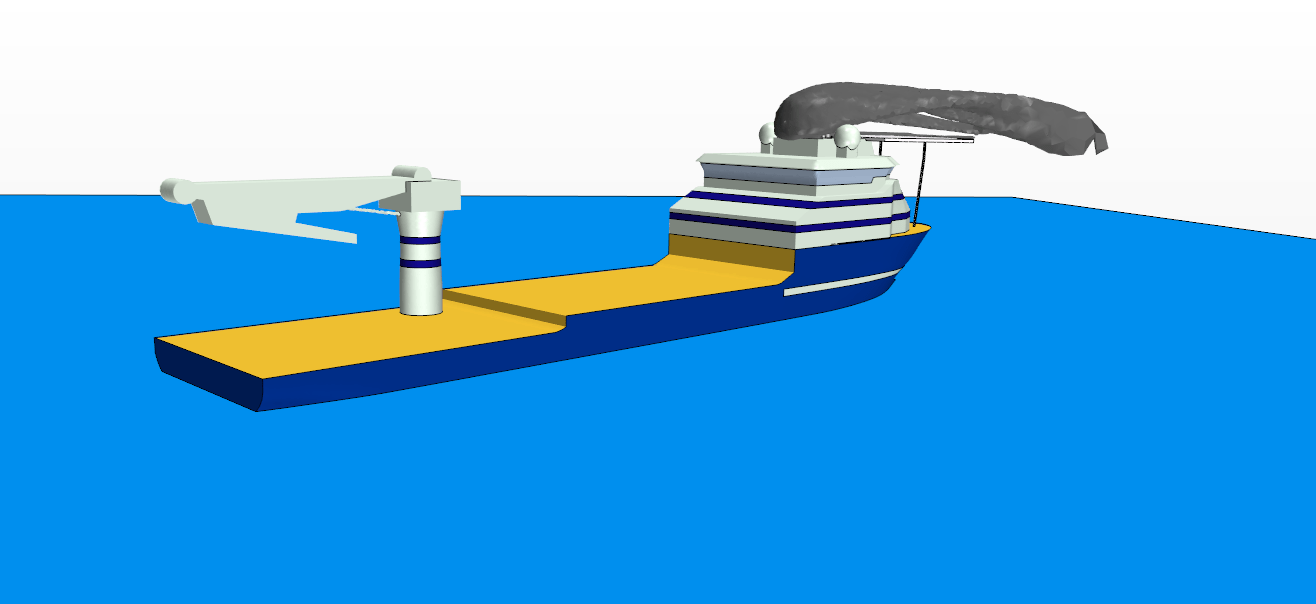