Ship propulsion engineering
Can we help you?
We’ll be pleased to answer your questions
CFD Hydrodynamics
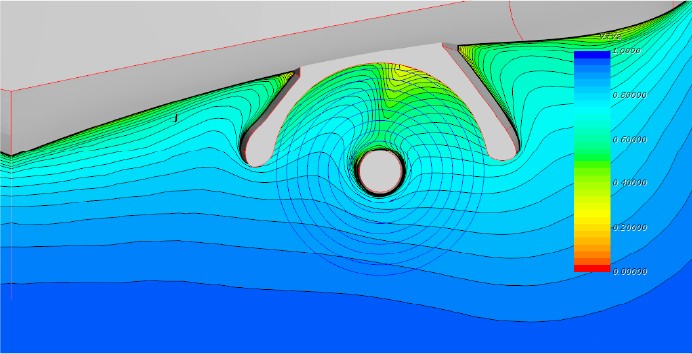
We are specialized on CFD hydrodynamics for ships
VICUSdt was the first engineering company specialized on ship propulsion engineering by CFD back in 2007. A huge experience accumulated together with more than 670 references on every ship type for hundreds of satisfied customers worldwide, ensures a good result.
Ship resistance and powering prediction
During the different stages of the ship design, the use of advanced CFD codes together with tools like NavCad allow VICUSdt to determine the resistance of the ship accurately, in still water or on any sea state, for bare hull or a complete hull with appendages. A correct powering prediction is the first step in a successful ship project. We carry out accurate ship powering prediction for leading engineering offices, shipowners and shipyards worldwide.
Ship model and most frequent sailing conditions
Displacement, trim and speed matrix
Optimal trim results for each scenario
Loading computer or dedicated interface
Trim optimization
- Merchant vessels can achieve significant savings with the correct trim for each displacement and speed.
- To do so, the crew must know beforehand how to load the ship depending on the expected speed and loading condition, to minimize ballast loading.
- VICUSdt carry out routine trim optimization calculations for merchant vessels, from small LPG to some of the largest container vessels in the world.
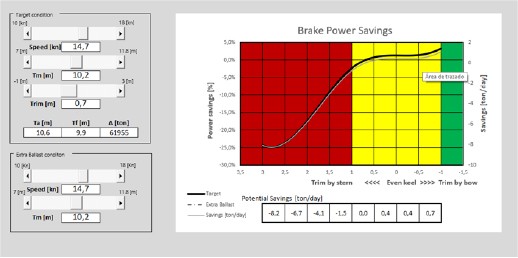
Wakefield and streamlines
The calculation and assessment of the flow arriving to the propeller is critical for a successful propeller design. A perfect knowledge of the nominal and effective wake allows a more adjusted propeller design, minimizing cavitation and increasing efficiency, resulting in significant fuel savings and a quiet propeller.
Hull form optimization
Improving the hull form design for minimum ship resistance in the different ship operational conditions, from trawlers to large container vessels. We have a multi-objective optimization methodology which together with the skills of our experienced naval architects guarantee the performance of your hull for every sea state. The optimization covers not only the bow, but also the ship aft body ensuring a good wake field.
For existing vessels we can provide new and optimized designs for bulbous bow or complete fore body, based on the real performance obtained from our monitoring or ship owner records, the design is tailor-made for the ship’s real operational profile, ensuring the best return of investment.
How can I improve my hull shape?
Autopropulsion and bollard pull analysis
We have a fully validated methodology for carrying out numerical self-propulsion tests with our CFD codes. Our experience in ship propellers and feedback from sea trials allow us to perform detailed predictions of the self-propulsion performance of any type of ship. We determine effective wake coefficients, thrust deduction, rotary-relative efficiency and overall propulsion performance in behind conditions.
The numerical self-propulsion simulation recreates the ship sailing with its designed propeller in such a way that the performance expected on its real life can be predicted with very high accuracy. The assessment of the thrust deduction factor is important for a redesign of the hull and modifications in the propulsion arrangement in such a way that the hull-propeller interaction is improved.
When it comes to bollard pull prediction, we have also validated our simulations with real tests performed on pusher boats, tugs and AHT. Do not play with the bollard pull performance of your ship, count on us during the project stage and avoid costly problems discovered during sea trials, when the solution will be much more complicated.
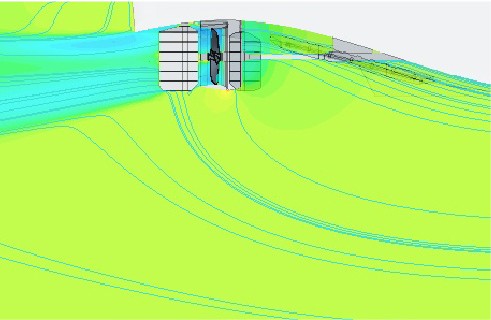
Moonpool and appendages
Appendages like bilge keels and gondolas should be aligned with the streamlines to minimize resistance and reduce turbulence.
Flow alignment is a critical issue for the gondolas on oceanographic and seismic research vessels. In this type of installations, we need to design and locate the gondola in such way that is free from air bubbles swept down from the free surface. An improperly designed gondola can result on a malfunction of the transducers, invalidating the main ship purpose of the vessel.
VICUSdt has participated in the hydrodynamic design of the most advanced oceanographic and seismic research vessels in recent years, including propeller design and complying with the underwater radiated noise regulation described in ICES 209 or DNV SILEN R.
The moonpool on offshore vessels and longliners can have a significant impact on resistance and air pumping effect of the raising water, these effects can be analysed in detail by CFD.