Ship propulsion engineering
Propeller shaftline analysis and design
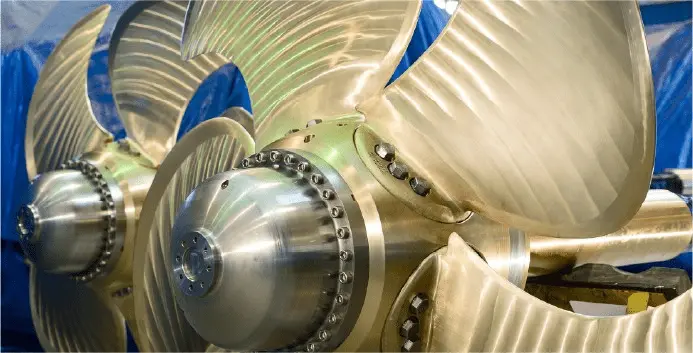
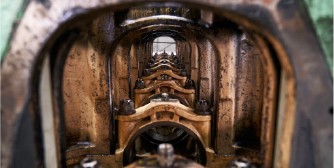
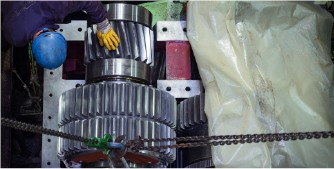
Shaftline design includes not only the sizing of the shaft, but its behavior under different load conditions in operation, including the various vibration modes of the system.
All the calculations for each shatfline
VICUSdt has a significant experience carrying out all the necessary shafting calculations for every type of propulsion shafting system for the most important Classification Societies and shipyards all over the world. Our reference list include every type of ship and propulsion configuration. It doesn’t matter if your project is retrofitting or newbuild, or if it is fitted with a direct drive or reduction gear, diesel or electric motor, thrust bearing, shaft brackets, oil or water stern tube, or any other feature. We definitely can help you with all the required shafting calculation and sea trial measurements for a detail evaluation.
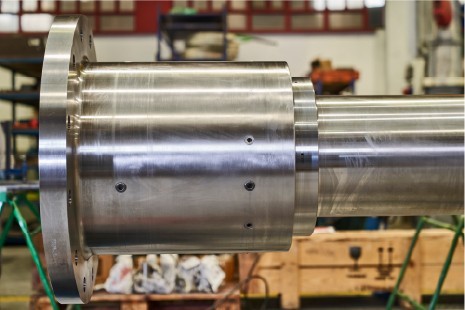
Under control shaftline alignment and vibration
Shaftline alignment and vibration problems can result in very serious damages in your propulsion system, forcing long downtime to carry out costly repairs.
“Control alignment and vibration in your shaftline to avoid costly damages”
Shaftline design
Besides a correct sizing of diameters, shaft line design takes also into account the shaft alignment and vibration analysis. The need of a correct lubrication of the bearing should also be bear in mind, so minimum shaft speed should be calculated. Sometimes, preliminary calculations should take place in the first stage of a project to make decisions about the number of bearings and their position as this can impact the project cost significantly.
Propeller shaft alignment
Not only for newbuilding, but also in retrofitting projects, shaft alignment calculation takes into account the characteristics of the shaft, the propeller and the hydrodynamic along with bearings particulars, gearbox elements and applied forces and flexible couplings in order to evaluate crucial aspects for the alignment:
- Loads share between bearings, and optimal positioning during alignment.
- Shaft slope (particularly in the aft-most bearing)
- Stress and deflection along the shaft
Alignment indications (bearing offsets, gap and sag values, jack-up instructions and expected load values) are given for a correct alignment procedure onboard.
Whirling, axial vibration analysis
Natural vibration frequencies of the system, both for lateral vibrations (whirling) and axial vibrations, should be considered to prevent early wear on bearings, noises, and damage on the shaft. These vibrations represent a source of fatigue loads which should be avoided to keep the resonance frequency of the shaft line away from the operating point of the system.
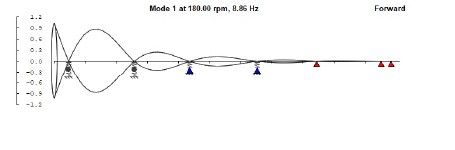
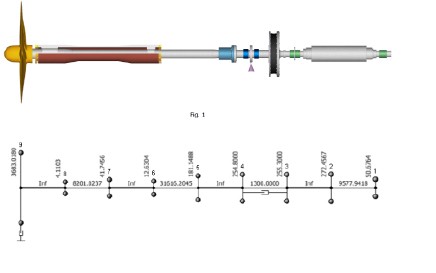
Torsional
Natural torsional frequencies related to the different running conditions (including misfiring) and their respective stresses can be evaluated through a mass-elastic system. In addition, ice impact transient torsional vibration can also be estimated to perform the complete shaft line design for ice-class vessels. Avoid costly troubles by evaluating your shaft line with a forced vibration analysis.