Ship propulsion engineering
Can we help you?
We’ll be pleased to answer your questions
CFD Aerodynamics
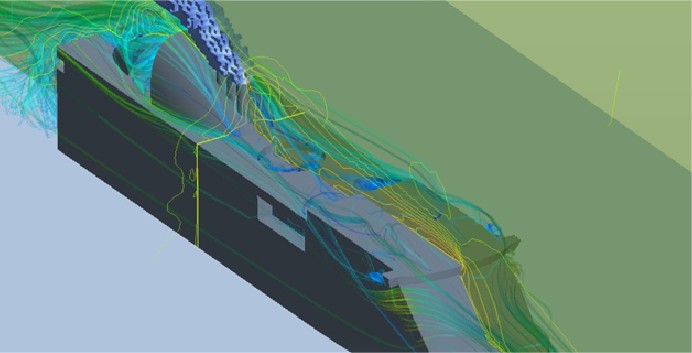
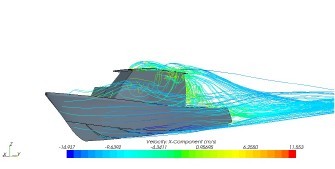
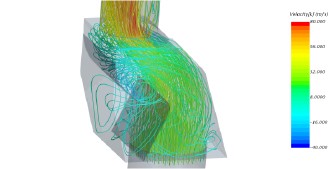
CFD airflow simulation in the ship
Aerodynamic CFD simulation allows us to analyze the behavior of the air over the vessel, as well as exhaust or ventilation gases in all types of ducts in a quick and reliable way.
Our CFD airflow simulation allows a precise calculation of aerodynamic forces and moments over the hull and superstructure of the ship.
When is it advisable to do a CFD aerodynamics analysis?
- Ship resistance. It can make a significant contribution on high speed boats.
- Docking maneuvers and sizing of tunnel thrusters.
- Dynamic positioning.
- Anchoring and mooring calculations. Useful when sizing mooring lines for instance.
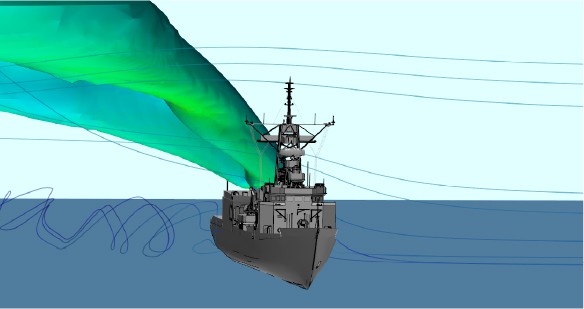
Exhaust gases and helideck
Calculating the trajectories and temperatures of the exhaust gas flow from the engines and how it interacts with other areas of the ship such as antennas, sensors, air intakes and helidecks by monitoring the evolution of the thermal plume.
Regarding the CFD calculation on helidecks, we apply the CAP 437, NORSOK C-004, HSAC RP or Brazil NORMAM 27 regulations in order to minimize the risk associated with the effect of wind turbulence and to ensure safe helicopter operations.
CFD Aerodynamics for Helidecks analysis
Helicopter landing in vessel decks is a critical operation.
Wind heading and intensity affect directly helicopter stability because strong gusts of winds produce so much turbulence in helidecks that it is impossible to operate.
Moreover, hot gases from ship exhaust funnels are also an important factor. If thermal rise between enviromental temperature and gases temperature is high, the helicopter will experience lift changes that can cause high instabilities, putting the operation at risk.
CDF aerodynamics simulations are very useful tool to develop these studies. They allow to reproduce the turbulence and temperature tendency that will experience the air close to the helideck. Air flow instabilities are produced by superstructure and thermal flow from exhaust funnels or by other thermal sources. CFD allows to study alternatives to mitigate both thermal and turbulence effect in landing zone.
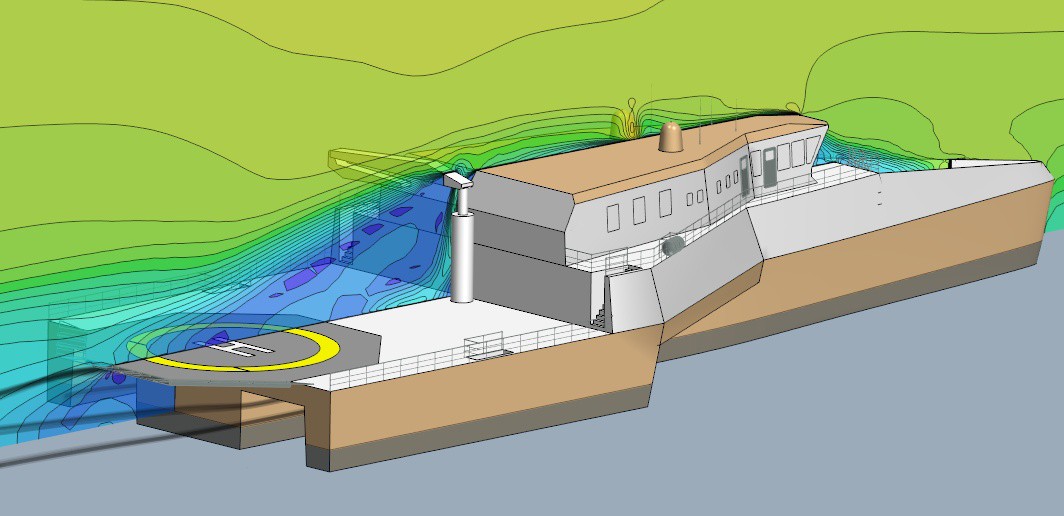
Safer helicopter landings
Achieve comfort with CFD aerodynamics simulations
The degree of aerodynamic comfort on balconies and terraces is verified through CFD simulations at the different speeds and directions of the ship, checking different variables such as turbulence, concentrations and odors of the exhaust gases at different points of the ship, as well as the increase in temperatures produced.
Comfort in crew or passenger accommodation areas is also checked by evaluating air velocity, temperatures and gradients, among other parameters.
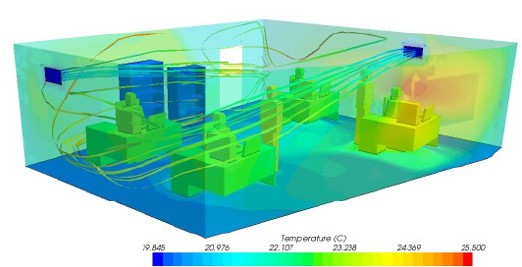
Ventilation in engine room, exhaust and HVAC pressure drop
Pressure drop in exhaust and ventilation ducts, as well as air distribution in engine room and other spaces including smoke dispersion on the garage of a RoRo for instance. We have experience modeling scrubbers, water separators, silencers and other components of exhaust lines. In addition, we can perform the coupled thermo-mechanical calculation CFD-FEM to evaluate stresses in the elastic support of the exhaust.
FAQs
CFD aerodynamics is the analysis of air flow around objects using numerical simulations. By employing computational methods to solve complex models, engineers can predict how air will interact with ship superstructures or within ducts. CFD aerodynamics is a powerful tool that enables the optimization of systems that involve fluid flow.
There are several types of CFD aerodynamics, each focusing on different aspects of fluid flow and its interaction with objects. It can involve external aerodynamics, which studies the flow of air around ship superstructures, or internal aerodynamics, which examines the flow of air within confined spaces such as ducts, pipes, and ventilation systems. Additionally, CFD aerodynamic studies can analyze laminar or turbulent flow, as well as compressible or incompressible flow. Finally, if the study involves the interaction of different phases of matter, such as liquid-liquid, liquid-gas, or gas-solid flows, it is considered a multiphase case. Each type of CFD aerodynamics can be adapted to the specific airflow problem that needs to be solved.
CFD aerodynamics can be applied to analyze airflow around vessels, offshore structures, buildings or any other types of objects. By establishing external wind load conditions, it simulates the interaction between the atmosphere and the object as realistically as possible. Such studies can yield important results, such as wind loads on structures or gas dispersion around the object.