Customer: e- Sea Tecnología de Propulsión
Related services: CFD simulation, propeller design
Scope of work
- Initial performance analysis by CFD
- Redesign and hydrodynamic optimization of geometry
Results
The company E-sea, has developed a small removable water propulsion system. The model is used on surfboards, SUPs, kayaks and all kinds of light boats. It consists of a waterjet powered by an electric motor and remotely controlled.
E-sea requested VICUSdt to optimize the hydrodynamics of the thruster. The objective is to improve the propulsive performance of the system trying to increase the thrust it provides and reduce the power required. This is intended to reduce energy consumption maximizing battery life and with it, endurance when sailing.
The optimization must be carried out maintaining the overall dimensions of the system and the rotational speed of the runner.
In a first stage, a series of CFD simulations are carried out on the initial geometry to identify how the flow behaves and possible areas for improvement.
Next, modifications are made in critical areas to study their influence and evaluate the progress made. A new propeller is designed, which maintains the number of blades and the rotational speed; varying their geometry, profiles and pitch distribution. A redesign of the nozzle is carried out trying to eliminate the recirculations and ensuring that the push created by it is favourable to the total thrust of the waterjet.
The last modification is to design a new stator. On the one hand, with the aim of directing the fluid downstream the propeller and having a more hydrodynamic discharge, recovering part of the lost rotational energy. On the other hand, it is intended that the thrust provided by the propeller increases with the integration of the stator, improving the degree of advance thereof. In addition, this element also provides a reinforcement to the set as a structural support.
The results of these modifications show a considerable improvement in the system, the new design offers a power reduction of 47% for the same thrust compared to the original.
Conclusion
After analysing the changes introduced, we incorporated the new propeller, the nozzle and the stator, keeping the original suction grid.
Recirculation detrimental to waterjet performance are eliminated, in addition, propeller performance is improved, and resultant thrust is increased, which results in more efficiency, significantly extending the life of the battery.
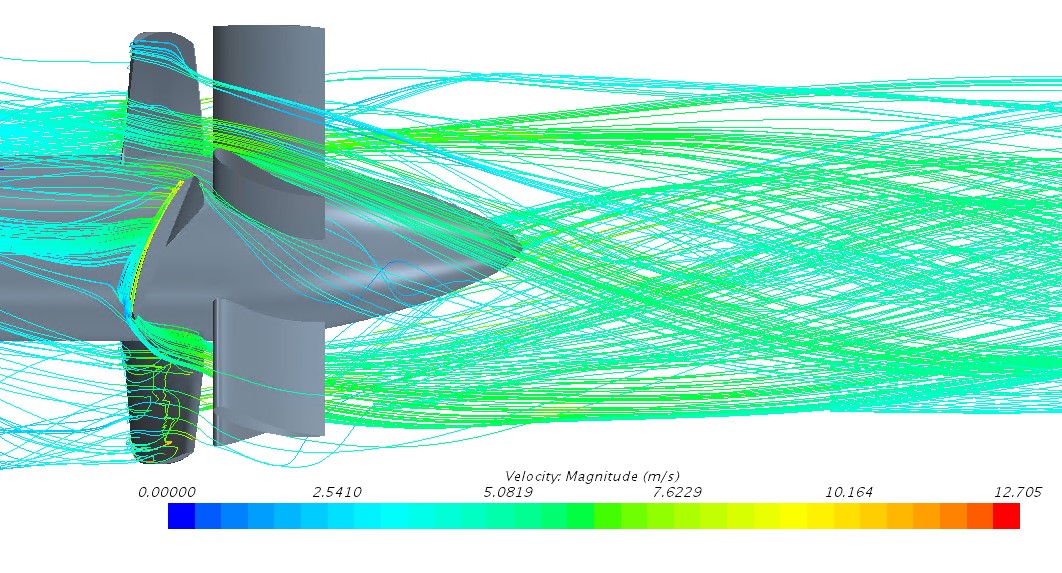
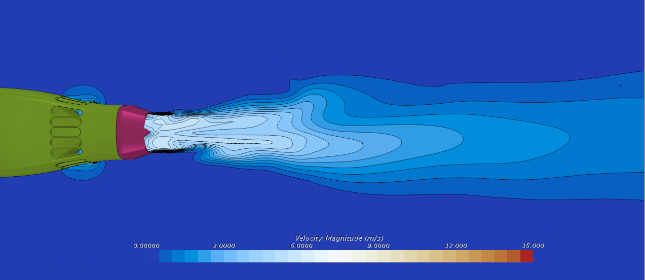
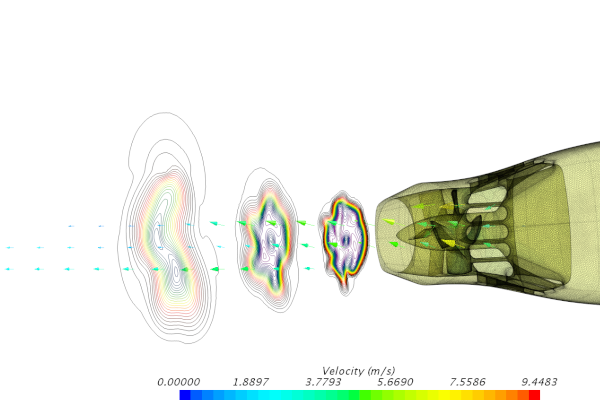
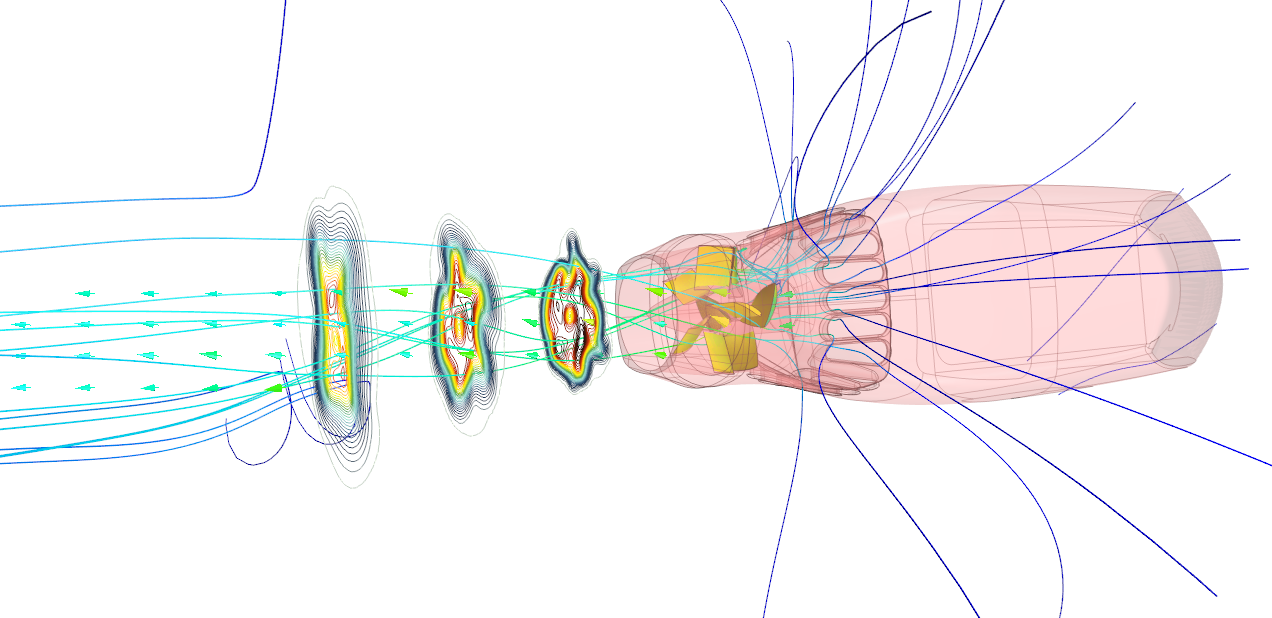
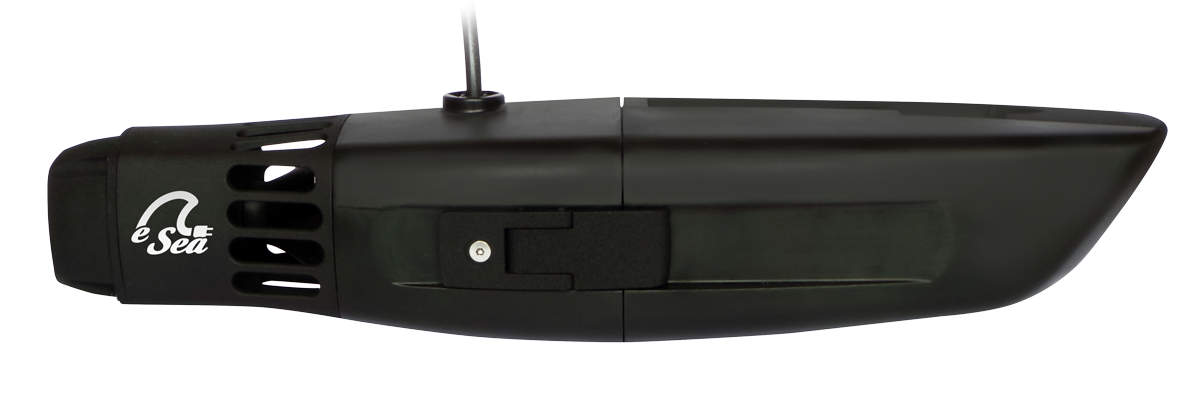
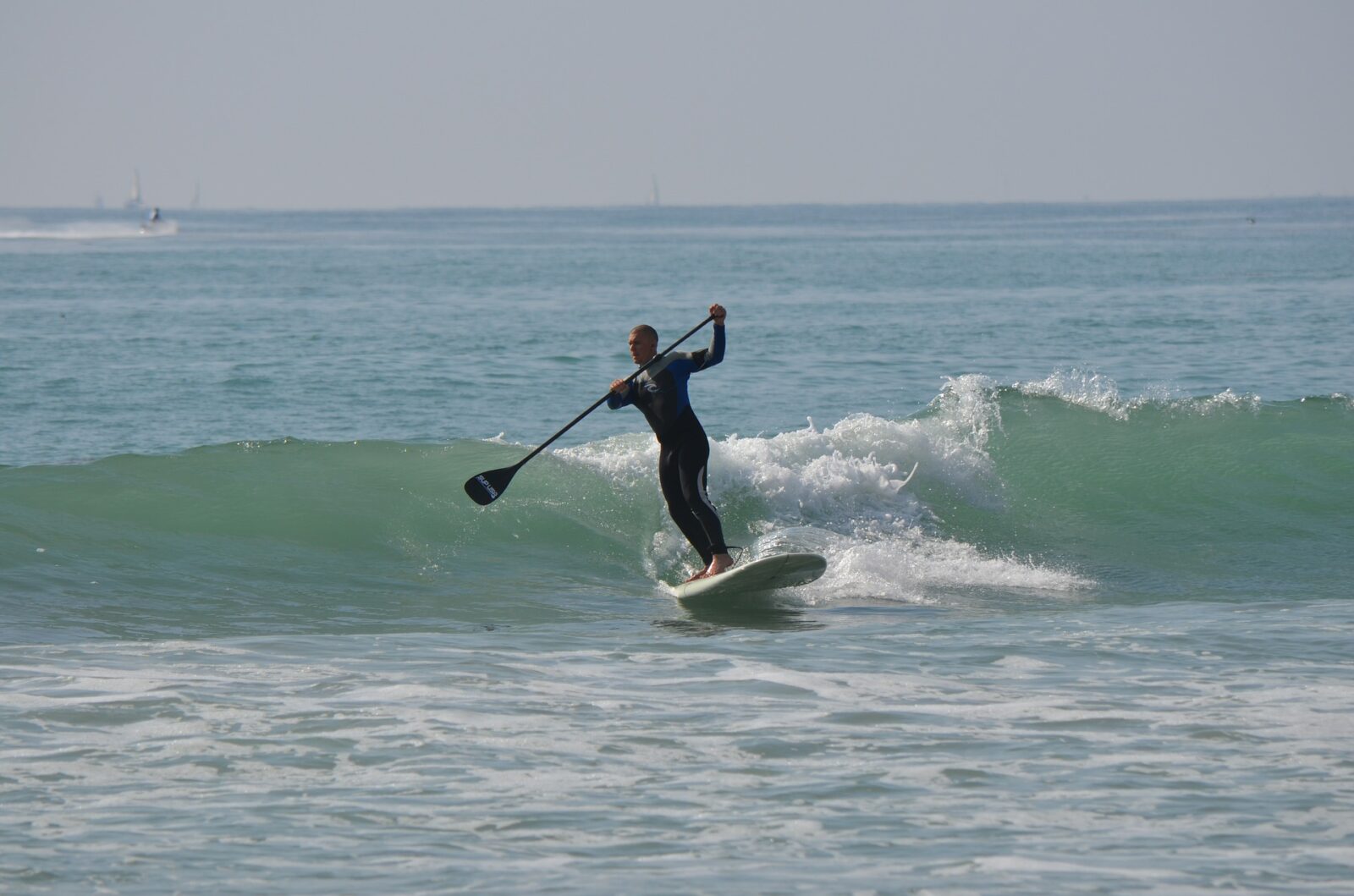
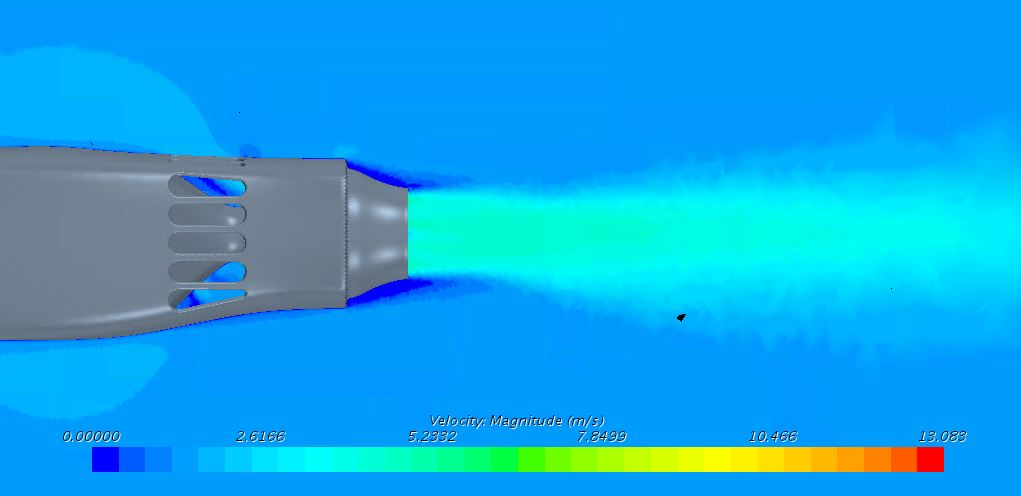
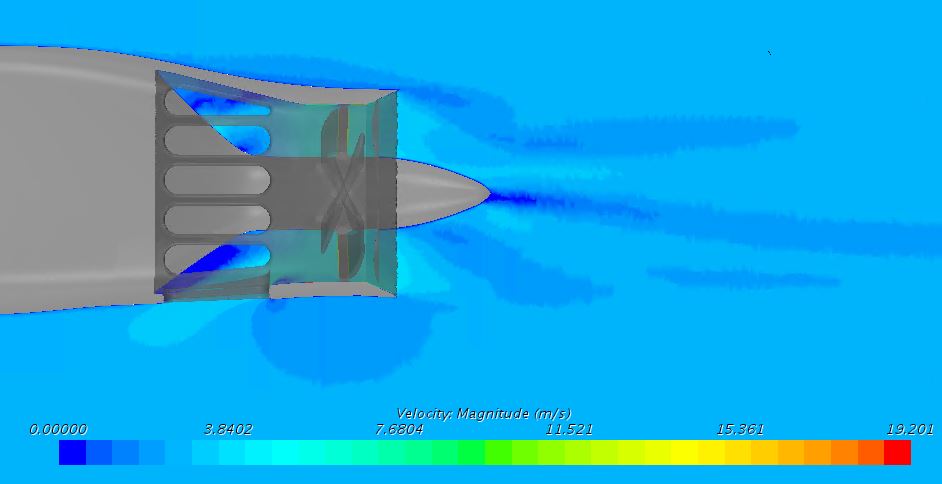
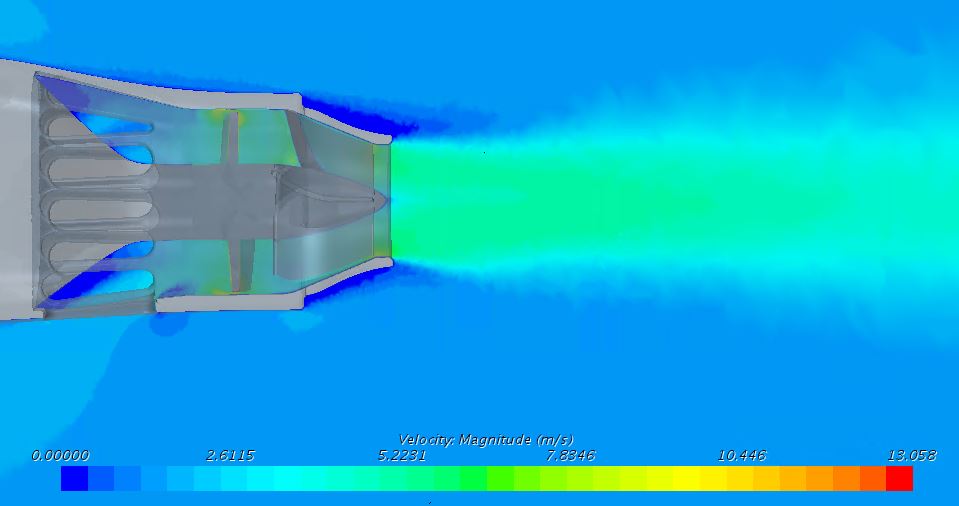
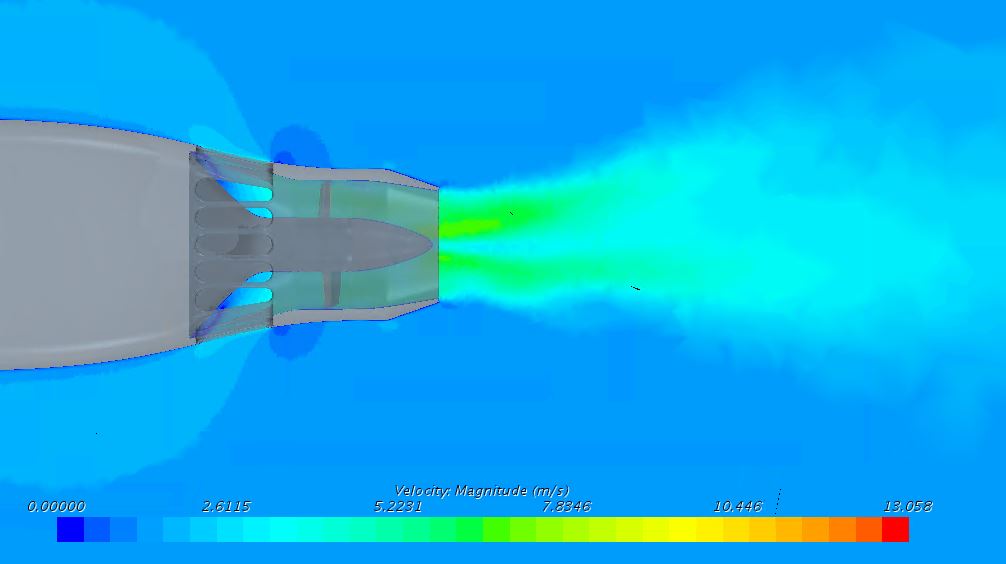
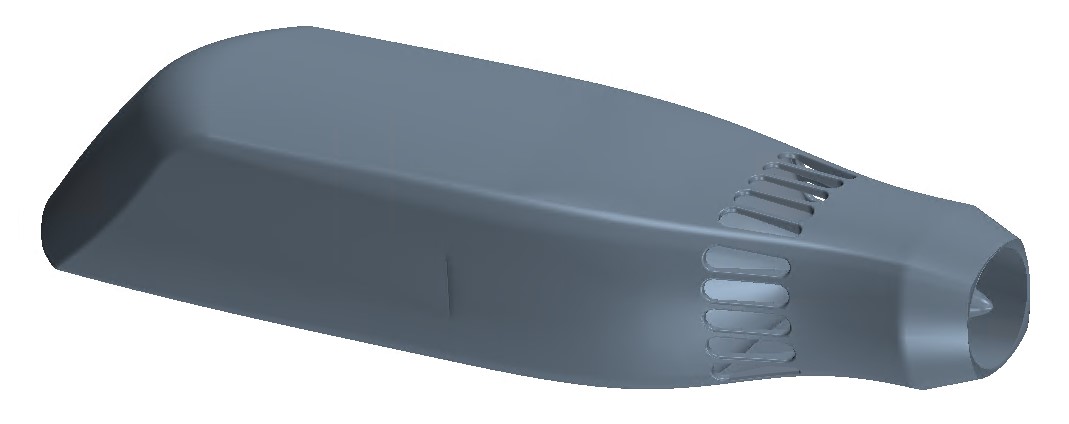
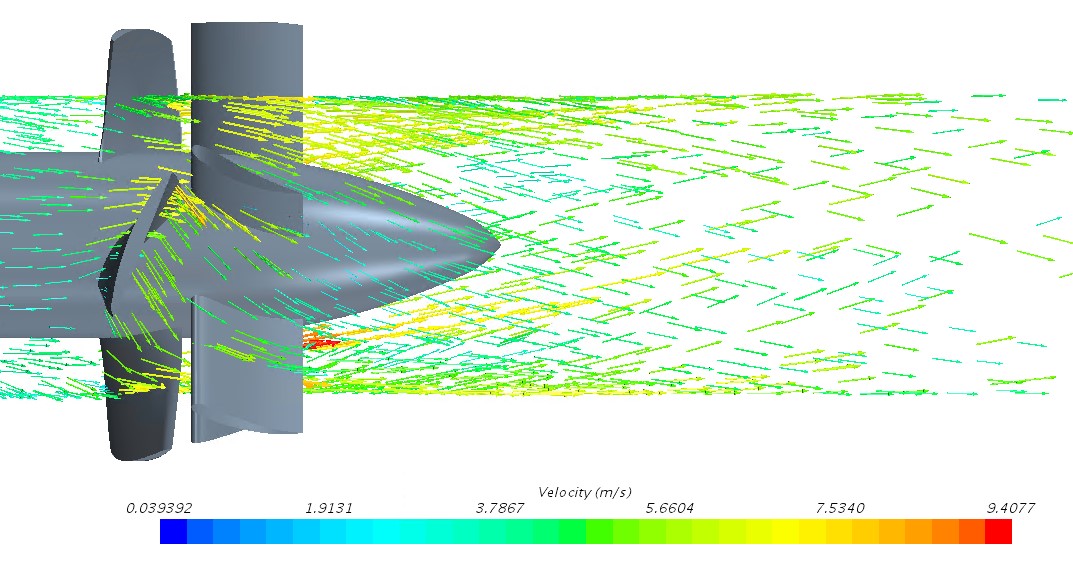

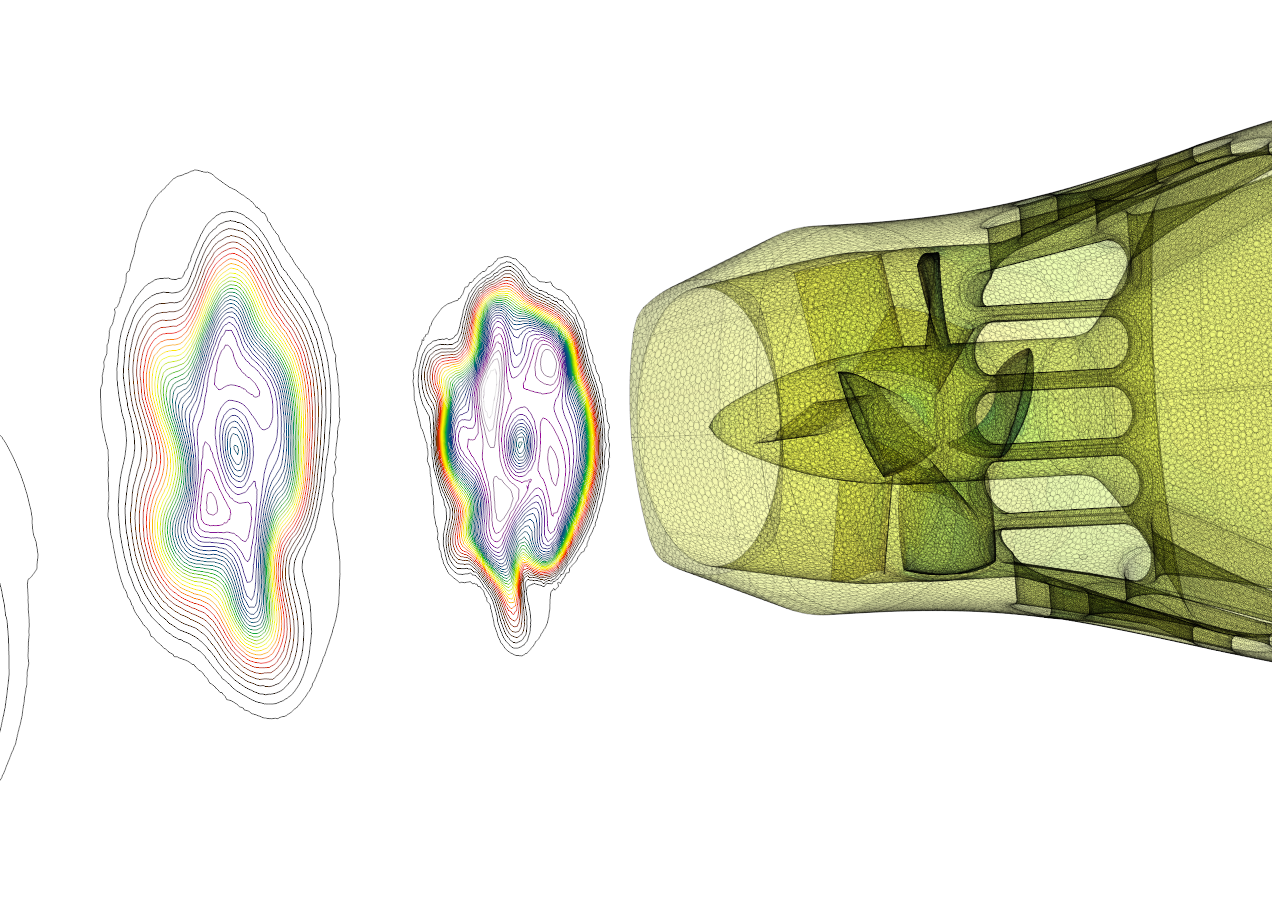
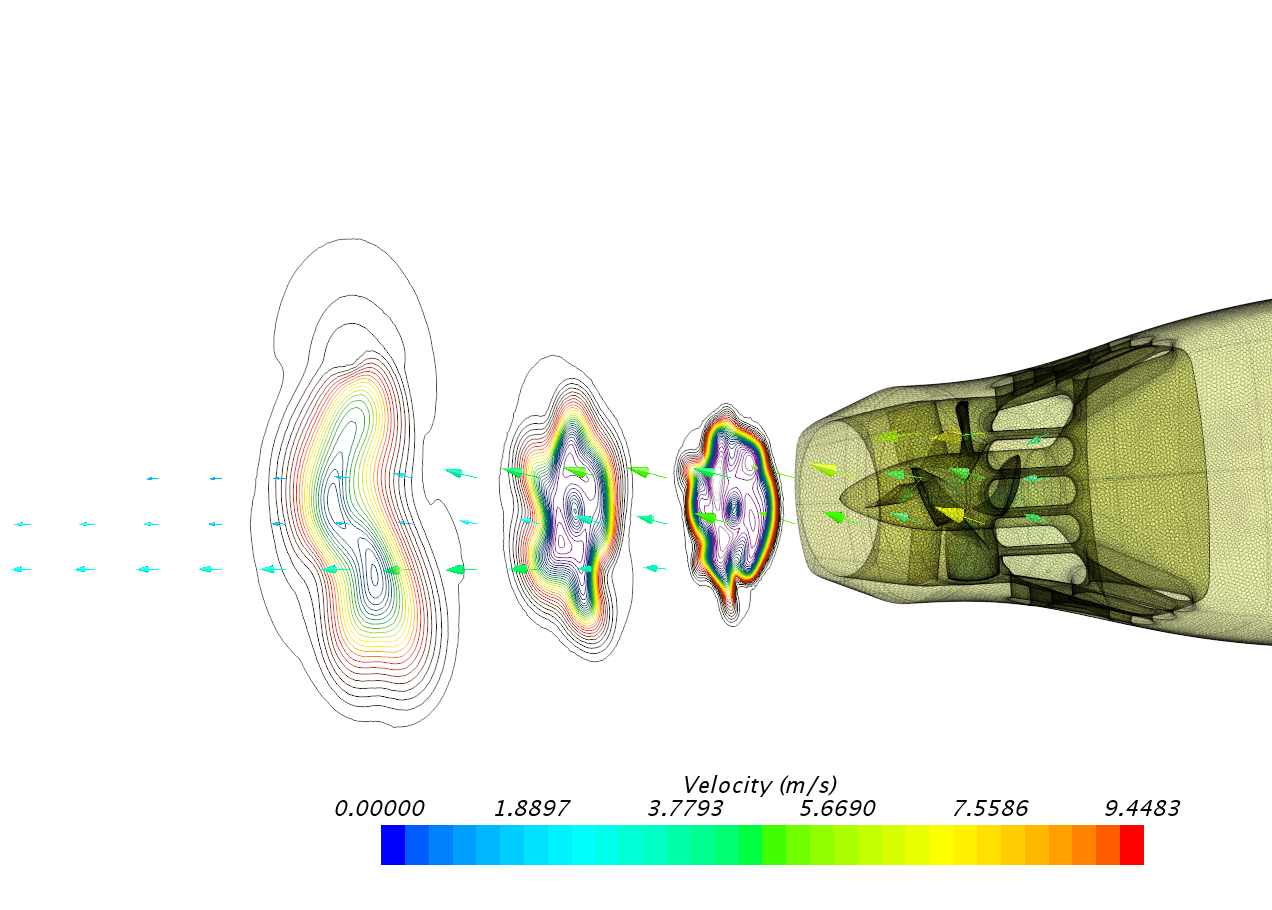
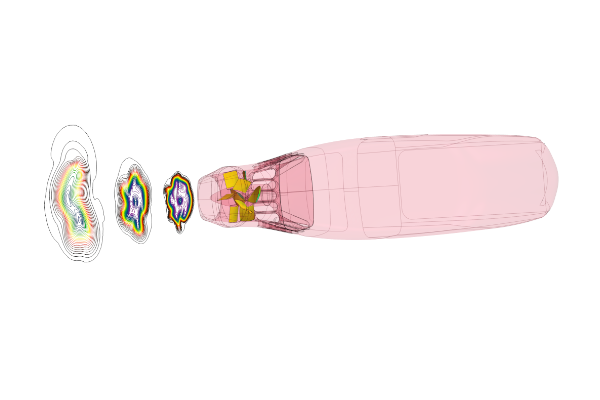
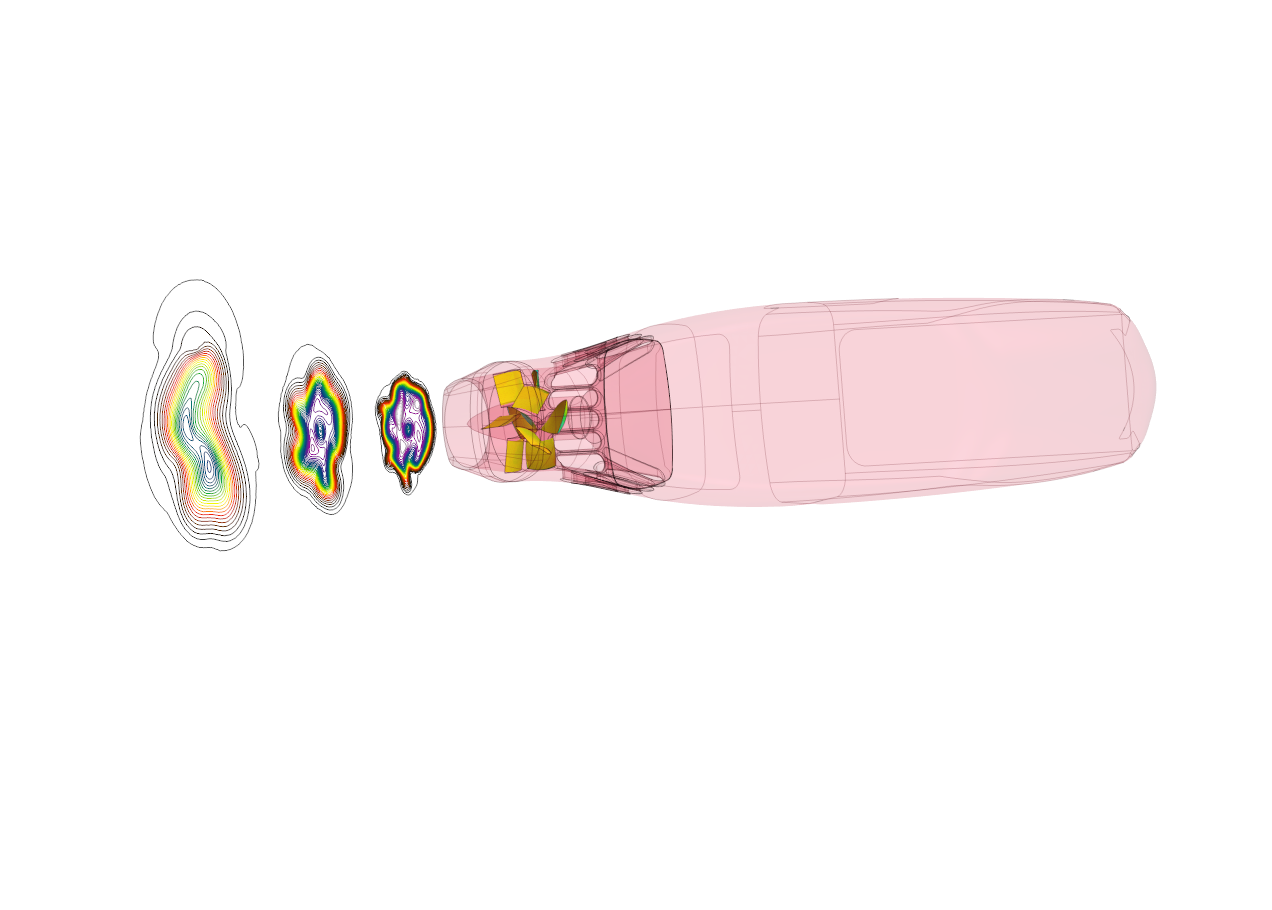
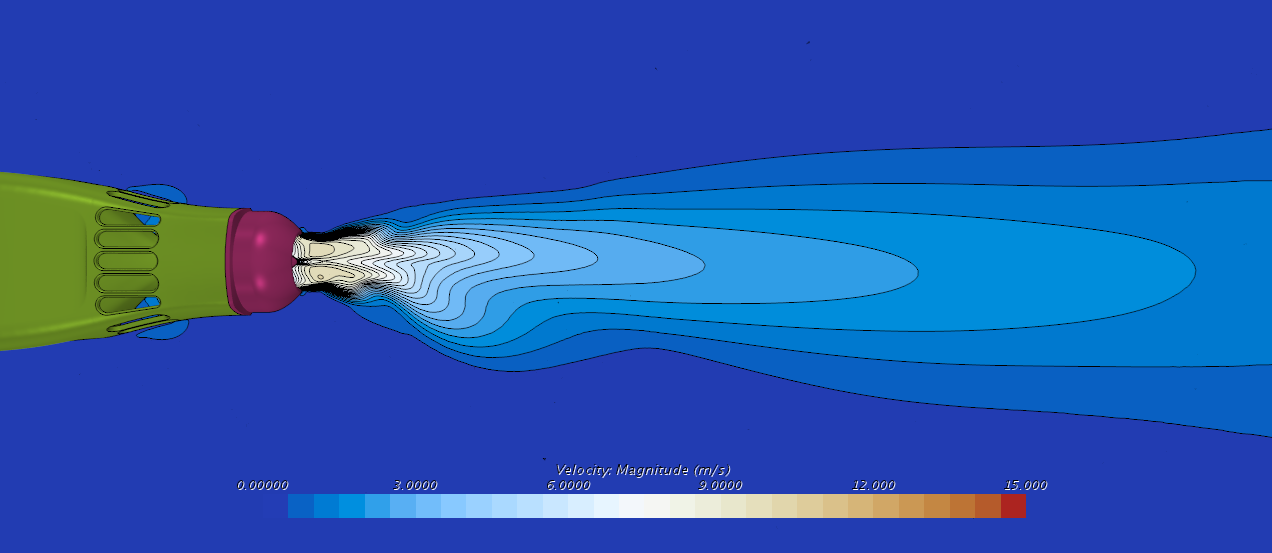
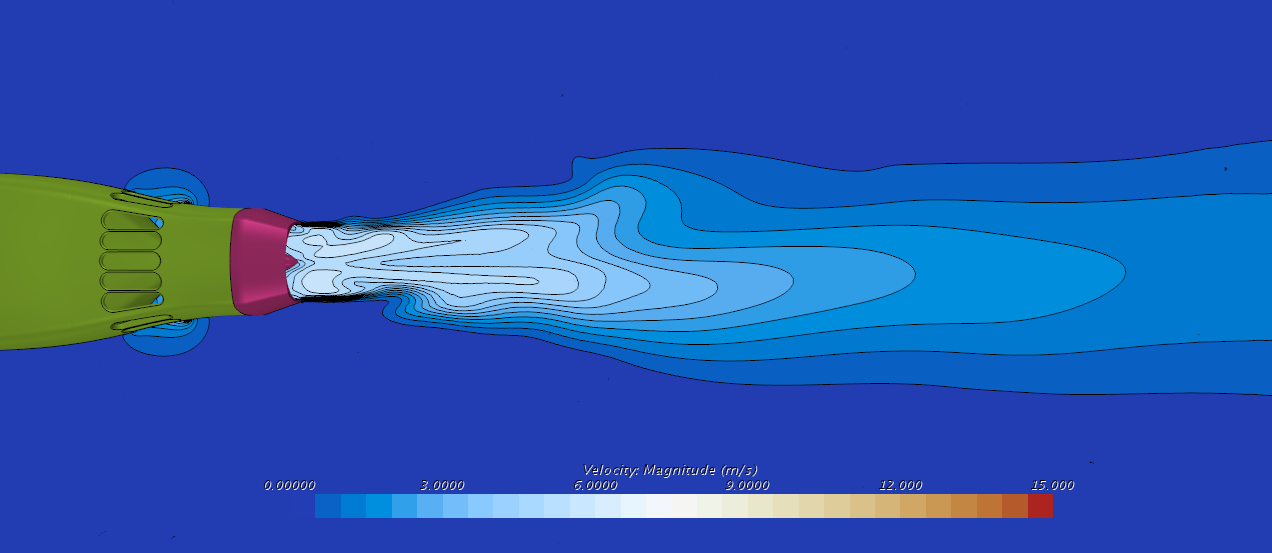
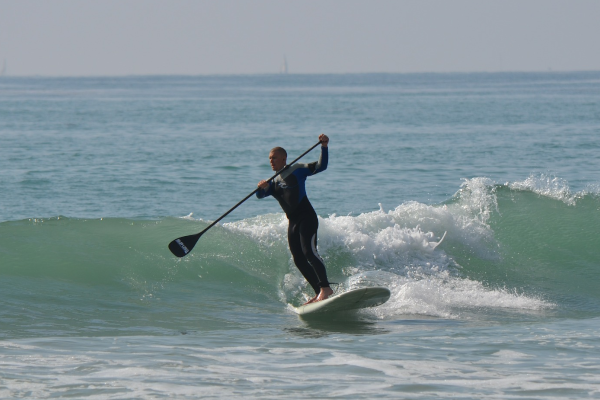
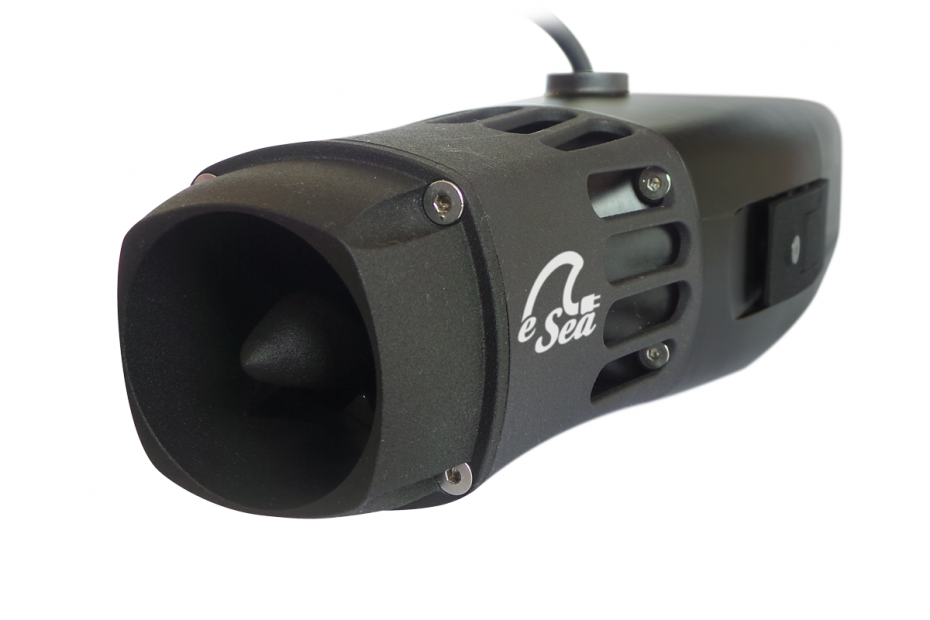