Ship propulsion engineering
Can we help you?
We’ll be pleased to answer your questions
CFD Hydrodynamics: Flow Simulation & Design Optimization
Computational Fluid Dynamics (CFD) hydrodynamics is an advanced technology for simulating and analyzing fluid behavior, essential in marine engineering for optimizing vessel performance. By using CFD hydrodynamics, engineers can precisely model how water flows around ship hulls, propellers, and submerged structures, allowing for in-depth insights into resistance, propulsion, and cavitation.
This technology enables the design of more efficient, eco-friendly vessels by minimizing drag, enhancing fuel efficiency, and improving overall operational performance.
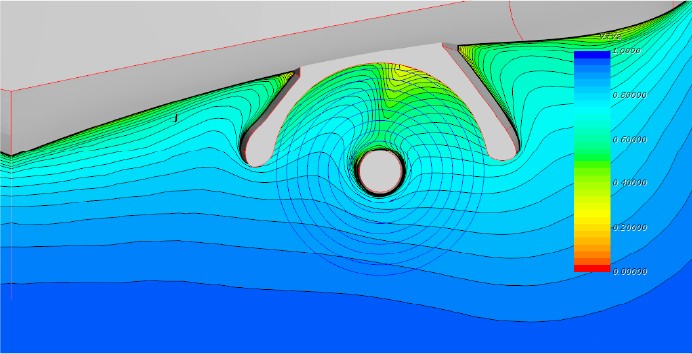
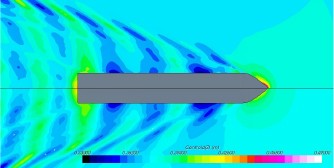
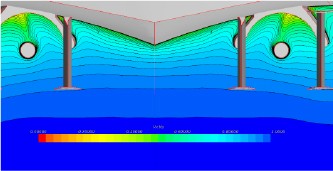
We are specialized on CFD hydrodynamics for ships
Since 2007, VICUSdt has led the field in CFD hydrodynamic analysis and ship propulsion engineering, becoming the first engineering firm specialized in these advanced techniques. With over 670 successful projects across all vessel types and a global portfolio of satisfied clients, our extensive expertise ensures precise and effective results in every project.
Naval hydrodynamics: Ship resistance and powering prediction
During the different stages of the ship design, the use of advanced CFD codes together with tools like NavCad allow VICUSdt to determine the resistance of the ship accurately, in still water or on any sea state, for bare hull or a complete hull with appendages. A correct powering prediction is the first step in a successful ship project. We carry out accurate ship powering prediction for leading engineering offices, shipowners and shipyards worldwide.
Ship model and most frequent sailing conditions
Displacement, trim and speed matrix
Optimal trim results for each scenario
Loading computer or dedicated interface
Trim optimization
- Merchant vessels can achieve significant savings with the correct trim for each displacement and speed.
- To do so, the crew must know beforehand how to load the ship depending on the expected speed and loading condition, to minimize ballast loading.
- VICUSdt carry out routine trim optimization calculations for merchant vessels, from small LPG to some of the largest container vessels in the world.
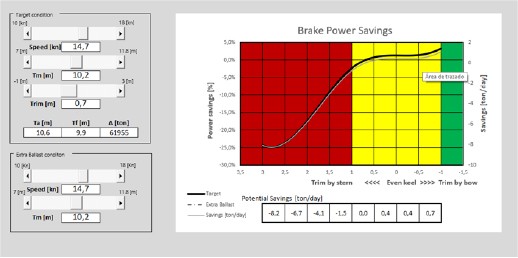
Wakefield and streamlines
The calculation and assessment of the flow arriving to the propeller is critical for a successful propeller design. A perfect knowledge of the nominal and effective wake allows a more adjusted propeller design, minimizing cavitation and increasing efficiency, resulting in significant fuel savings and a quiet propeller.
Hull form optimization
Our hull form optimization services focus on designing hulls with minimum resistance across diverse operational conditions—from trawlers to large container vessels. Using a multi-objective optimization methodology and the expertise of our seasoned naval architects, we ensure top performance in every sea state. This optimization process covers not only the bow but also the aft body of the ship, resulting in a smooth wake field and enhanced overall efficiency.
For existing vessels, we provide optimized designs for the bulbous bow or the complete forebody, tailored to real performance data gathered from onboard monitoring systems or shipowner records. By aligning the design with the vessel’s specific operational profile, we ensure maximum efficiency and a strong return on investment.
How can I improve my hull shape?
Autopropulsion and bollard pull analysis
We offer a fully validated methodology for conducting numerical self-propulsion tests using advanced CFD codes. With extensive expertise in ship propellers and insights from sea trials, we provide precise predictions of self-propulsion performance for all vessel types. Our simulations accurately determine key parameters such as effective wake coefficients, thrust deduction, rotary-relative efficiency, and overall propulsion performance in real-world, behind-hull conditions.
Our numerical self-propulsion simulations replicate the vessel sailing with its designed propeller, allowing highly accurate predictions of its real-life performance. Assessing the thrust deduction factor is crucial, as it informs any necessary hull redesigns or propulsion system adjustments, optimizing hull-propeller interaction for maximum efficiency.
For bollard pull predictions, we’ve validated our simulations through rigorous real-world testing on pusher boats, tugs, and AHTs. Don’t leave bollard pull performance to chance—partner with us during the project stage to avoid costly issues that could arise during sea trials, when solutions are far more complex and expensive to implement.
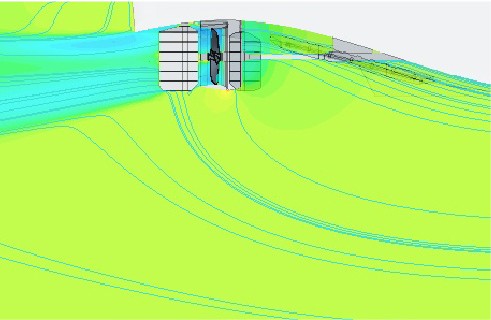
Moonpool and appendages
Appendages like bilge keels and gondolas should be aligned with the streamlines to minimize resistance and reduce turbulence.
Flow alignment is a critical issue for the gondolas on oceanographic and seismic research vessels. In this type of installations, we need to design and locate the gondola in such way that is free from air bubbles swept down from the free surface. An improperly designed gondola can result on a malfunction of the transducers, invalidating the main ship purpose of the vessel.
VICUSdt has participated in the hydrodynamic design of the most advanced oceanographic and seismic research vessels in recent years, including propeller design and complying with the underwater radiated noise regulation described in ICES 209 or DNV SILEN R.
The moonpool on offshore vessels and longliners can have a significant impact on resistance and air pumping effect of the raising water, these effects can be analysed in detail by CFD.