Ship propulsion engineering
Special CFD simulations
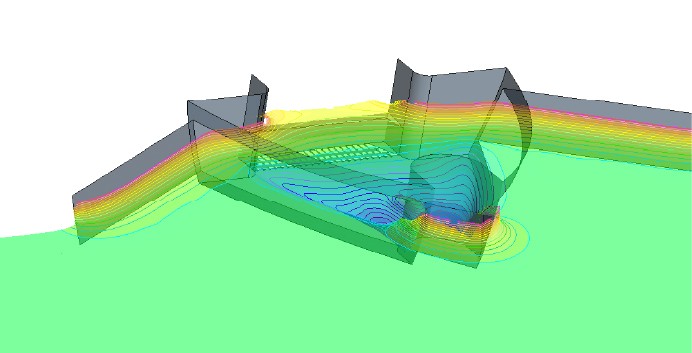
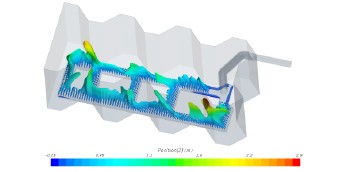
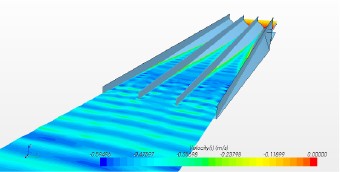
And we are not only experts in ship propulsion systems, we can analyze other types of fluid dynamic problems in ships.
What other fluid dynamic problems do we deal with at Vicusdt?
- Sea chests
- Box coolers
- Scrubber water cleaning
- Side discharges
- Oil recovery
- RSW tank flow, etc.